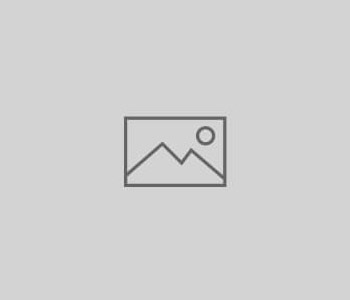
Mission Table – Part 2 – Mortise and Tenons
Last time we covered the initial design and milling, so let’s get started cutting some joinery! The arts and crafts and mission style furniture is known for its mortise and tenon joints and there are almost 30 of them in just this small table. I’m certainly not going to show you all of them, considering they’re all cut pretty much the same way, but I will mention a few tricks.
The first trick to make things a little easier on yourself is mainly for hand tool users – it’s to size your tenons to your chisels. I used just two mortise chisels for this whole table, a ¼” and a ⅛”, and I set my marking gauge to the chisels size and used it for everything. This makes cutting the mortises a lot easier.
There are a thousand ways to cut a tenon and almost as many tutorials out there, so I won’t get into the specifics of how I saw them, but one of the things I like to do is use deep marking lines and make knife walls. This helps guide the saw and gives me a nice crisp line to pare down to with the chisel at the end.
For the small dovetail on the top rail I just cut the rough shape with a chisel, don’t worry about the saw – nobody is going to see this joint anyway.
I use the same marking gauge to mark my mortises, so I know they’ll be consistent. Again, I won’t go into specifics about the mortising process, there are plenty of tutorials out there that do a better job explaining it than I can, but one thing I like to do is to make a few shallow chisel grooves at first, just to create a little well to help guide you lining up the chisel when you start hammering.
I should also mention my setup – it’s never a good idea to hammer directly in the vise, so I clamp a piece of scrap wood in the vise, then clamp my piece to that, so that the workpiece is over a leg and held tight. I also use the scrap piece as a vertical guide for the chisel to make sure I’m straight up and down.
As I hammer across the length of the mortise I’ll leave about an ⅛” of an inch on both sides so that when I pry out the waste I don’t bruise the ends too much. This isn’t such a big deal on this piece because they’ll be hidden under the shoulders of the tenon, but it’s a good habit. I also have a sharpie mark on the chisel to know when I’m down to the correct depth.
During the test fit – one of the joints was a little bit too tight and a few swipes with a block plane fixed that. If it was a larger tenon I may use a shoulder plane to thin it down some.
And there we go for most of the joinery – I think 28 mortise and tenon joints total and then a single dovetail for the top rail on the front. This should hopefully keep the front from bowing out at all. The tenons on the aprons did overlap a little, so with a block plane I mitered those ends just a little bit.
Now I’m getting ready for pre-finishing with some smooth plane work – notice that I’ve taped over the glue surfaces so no finish gets in the way of the joints.
The next step is the panel joint for the top. If you plane both pieces at the same time it makes this joint super simple – this edge doesn’t even have to be square to the faces since any error will be off-set by the mirrored piece.
To check the fit, just “un-fold” the two pieces and see how they line up. I aim for a very slight spring to the joint that’ll close up with clamps.
I’m going to go ahead and glue up everything before I build the drawer, just because I want that fit to be right. But before I glue everything up, I’m going to pre-finish everything. This is a three step, super easy recipe from Bob Lang. The first coat is Varathane “Special Walnut” stain to darken everything.
The second step is a coat of Watco “Dark Walnut” danish oil to give it a little more tint.
The last step is a coat of amber shellac to warm everything up a bit.
Next time we’ll add some of the internal pieces and finally do the drawer. So that’s it for this time!